Siemens Leading the Way Towards the Industrial Metaverse
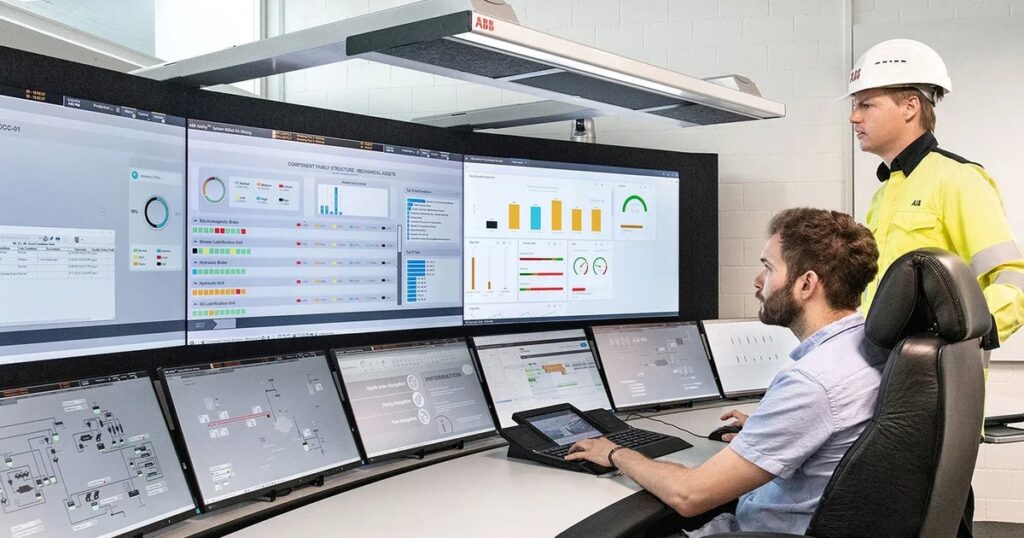
The Benefits of VR Training
Safer and cost-effective : A controlled environment lacking real-world risks and costs
Interactive and immersive: A hands-on experience without distractions
Customisable: Programmes can be tailored to roles, machinery and procedures
Flexible and accessible: Can be conducted remotely at any time
Virtual reality training will also help attract future talent, according to Bart. With the World Economic Forum predicting a shortage of over 7 million skilled manufacturing workers by 2030, this talent is greatly needed.
“For attracting new talent, especially younger generations who are tech-savvy and accustomed to digital experiences, VR training presents the industry as forward-thinking and innovative,” he says.
“It demonstrates a commitment to cutting-edge technology and continuous learning, making the manufacturing sector more appealing. Additionally, the flexibility and accessibility of VR training can draw individuals from diverse backgrounds, broadening the talent pool and fostering a more inclusive workforce.”
VR training also enhances the upskilling process and increases the accessibility of specialist manufacturing knowledge, helping to achieve the vital task of plugging manufacturing’s knowledge retention gap.
“Today’s mobile generation of workers are more likely to jump between different companies and process areas, so it’s highly important that we plug the knowledge retention gap that this can leave in a business,” says Sanjit Shewale, Global Head of Digital Business Line, ABB Process Industries Division.
“Equipping human operators with the skills to work with autonomous technology is essential to continuously evolve the AI/ML models that have been built using the invaluable human knowledge embedded within them. Arming workers with these skills in the digital age is not a matter of choice: it’s a necessity.”
Siemens shares this perspective, leveraging VR technology to drive broader industry digital transformation.
“Siemens’s commitment to integrating advanced technologies into its training programmes underscores its dedication to future-proofing the industry,” says Bart.
Another way the company is future-proofing the industry and embracing the digital metaverse is through reimagining the factory itself with the Omnifactory.
The impact of the Omnifactory
There’s plenty of talk in the manufacturing sector about the ‘factory of the future’. But what’s often missed in these discussions is the need for a fundamental rehaul of how we conceptualise, build and expand factory operations.
Industry 4.0 is being implemented into a foundation designed for the manufacturing needs of the late 20th century – not a factory designed with today’s supply chain unpredictability, ebbing and flowing demand and digital transformation in mind.
Siemens has said it is time for a redesign, with the Omnifactory, a holistic factory of the future that advances the importance of the industrial metaverse.
“The Omnifactory is a five-year project at the University of Nottingham which comprises hardware from multiple sources connected on a backbone of Siemens hardware and software to create a step-change in manufacturing for companies large and small,” says Bart.
“It represents a next-generation manufacturing environment where digital and physical worlds converge, enabling a fully integrated, smart production ecosystem.
“This initiative showcases advanced technologies such as IoT, AI, and digital twins, highlighting Siemens’s commitment to innovation and excellence in manufacturing.”
As consumer demand for personalisation grows, the Omnifactory helps manufacturers transition from the traditional factory focus of high volume and low complexity to prioritising flexibility.
Using the Siemens Xcelerator portfolio, a digital twin of the manufacturing process is generated, optimising operations, eliminating waste and lessening the demands of testing through ‘virtual commissioning’. With digital twins, prototypes are unnecessary.
Additionally, the Omnifactory is furthering student research and understanding of manufacturing, something which Siemens also seeks to do through its comprehensive micro-credential programmes.
“Through micro-credential programmes, Siemens offers targeted, specialised training that allows employees to gain specific skills and certifications,” Mark explains.
“Partners for this include the University of Colorado Boulder and Pennsylvania State University. These programmes are designed to be flexible and accessible, accommodating the varied needs of the modern workforce.”
“By providing these opportunities, Siemens not only upskills its current employees but also attracts new talent by offering clear pathways for career development and continuous learning.”
The Omnifactory comes with scalability built-in, capable of implementation across small and large operations. Siemens assists both large manufacturers and SMEs with implementing the key principles of the Omnifactory to repurpose their facilities and respond faster to changing market demand.
Ultimately, Siemens seeks to commodify the Omnifactory processes so all of global manufacturing can take advantage, driving future opportunities.
“The future of manufacturing is already here and it provides abundant opportunities for manufacturers to further excel in their markets,” adds Ajithkumar.
“The winners of this exciting era would be the true pioneers and, as the saying goes ‘The best way to predict the future is to invent it’.”
Source link
#Siemens #Inventing #Future #Industrial #Metaverse